iStock-938708276
By: Editorial team
Reading time: 7 Minutes
◤ COVER STORY
How can steelmaking generate less CO₂?
What can the steel industry do to help reduce CO₂ emissions? “Green steel” is possible, but it will take more time and extensive development. Efficient combustion processes can already reduce emissions. Oxygen makes the difference here.
When the topic of discussion turns to 21st-century industry, people first think of microelectronics, smart plastics and biotechnology. Before such products can be made, however, raw materials must be mined, energy generated, machinery manufactured, warehouses built and a whole lot of precursors and intermediates have to be transported – often the world over. The oil platforms, gas pipelines, wind and water turbines, production machinery, buildings’ structural framework, storage racks and huge container ships are all mostly made of steel. The same goes for our cars and for the load-bearing elements of bridges and skyscrapers. Steelworkers thus supply the most important raw material of our modern world.
According to the industry group World Steel Association, the world produced 2.1 billion metric tons of steel in 2022 – and more than half it was manufactured in China. About 3.6 billion metric tons of carbon dioxide were emitted to the atmosphere as a result. That represents about nine percent of global CO₂ emissions due to human activity. The decarbonization of the steel industry is essential to achieving the Paris climate goals. Moreover, the still freely available emission rights in Europe will expire in 2034. Based on today’s figures, this could cause European steel manufacturers’ profits to collapse by about 70 percent if they have not dramatically reduced their CO₂ emissions by then.
CO₂ emissions in different steel process routes
There are two fundamentally different types of conventional steel production, which also differ significantly in terms of their CO₂ footprint. In the primary integrated process route, the steel is produced from iron ore and coke in blast furnaces. The complete process route comprises coking plant, sinter plant, blast furnace, converter and the subsequent stages of casting and forming. On average, 1.9 tons of carbon dioxide are released per ton of steel produced. The largest share of those emissions are associated with the blast furnace.
The secondary route uses an electric arc furnace instead of a blast furnace, and scrap instead of iron ore. At a rate of 0.4 tons of CO₂ per ton of crude steel, it emits far less greenhouse gas. And most of that CO₂ comes from fossil fuel-based electricity production, which can generally be converted to renewable energy sources.
So would opting for the secondary route using renewable energy solve the problem? No, unfortunately not. For one thing, there is not sufficient scrap everywhere. In China, for example, only 10 percent of steel comes from recycled material. Moreover, some high-quality flat steel grades cannot be produced by the secondary route.
Since the early 1970s, however, direct reduced iron (DRI) has offered a third process route, which is already widely used today in some countries, such as India. In recent years, numerous pilot projects have proven that production of the synthesis gas required for this process can be gradually converted to pure hydrogen and that, in combination with the electric arc furnace method, DRI can replace the integrated primary route. When the required electrical power is supplied from renewable sources, this method can produce steel with almost no greenhouse gas emissions at all (net zero emissions).
The availability of electrical energy produced without CO₂ emissions is a basic prerequisite in nearly all future processes. Several decarbonization technologies are currently in various stages of development and can be combined with one another:
Reduction of CO₂ emissions (smart carbon usage)
- Increased energy efficiency (e.g., with oxyfuel)
- Use of low-CO₂ fuels
- Injection of biomass and H₂ into the blast furnace process (with hot gas recirculation)
- CO₂ capture (carbon capture, utilization and storage, CCUS)
Avoidance of CO₂ emissions (carbon direct avoidance)
- Integrated direct iron reduction with hydrogen (DRI plus electric arc furnace or electric low-shaft furnace)
- Electrolysis of iron ore
Long haul to green steel – projects in Europe
“Over the long term, we can completely decarbonize with green steel, but for the moment it’s barely a drop in the bucket,” explains Davor Spoljaric, Senior Vice President Applications at Messer. “To produce it in large quantities, not only will new technologies have to be developed, but sufficient volumes of green hydrogen will also have been available. In both respects, we’re still in the early stages.
The EU already recognized decades ago that the steel industry’s emissions would pose a major problem in the future. Together with the steel industry, it initiated the Ultra-Low CO₂ Steelmaking (ULCOS) research project. In 2020, the world’s first “fossil-free iron ore” pellets were produced in Luleå, Sweden. That’s the site of the HYBRIT project pilot plant, a joint venture operated by steel and energy industry companies. This Hydrogen Breakthrough Ironmaking Technology test run can certainly be regarded as a first breakthrough. Industrial-scale production is scheduled to begin in 2026; if all goes well, the new technology will reduce Sweden’s CO₂ emissions by ten percent and Finland's emissions by seven percent starting from 2035. To ensure an adequate supply of green hydrogen, however, renewable energy production and water electrolysis capacities must be hugely expanded. Even if everything goes according to plan and other countries follow the Scandinavian pioneers’ lead as soon as possible, it will take decades to implement this conversion.
The EU specified the most important interim step with the stated goal of reducing Europe’s total emissions to 55 percent of the 1990 level by 2030. To achieve that goal, the steel industry must cut its emissions by at least 30 percent. According to estimates by Boston Consulting Group, this would require replacing one third of all blast furnaces with direct reduction units like the ones ThyssenKrupp and Salzgitter want to build in the next few years. In Austria, the supervisory board of voestalpine gave the green electric light in March 2023 for the first 1.5 billion euros of investment that will be used to replace Austria’s conventional steel production with DRI and electric arc furnaces (greentec steel). There are 24 DRI projects in the planning or construction stages in Europe today – with a total production potential of 40-50 million metric tons of steel and an energy requirement of about 400 terawatt-hours. And because about half of Europe’s steel production capacity today will reach the end of its service life by 2030 anyway, the new H₂-DRI plants represent a great opportunity for climate-friendly reinvestment.

❝
To reduce CO₂ emissions in the near term, however, we also have to examine the existing processes and technologies,” insists Davor Spoljaric. “There’s a considerable potential there for measures that require relatively low investment and can be implemented rapidly.
Davor Spoljaric, Senior Vice President Applications at Messer
Possible immediate action
“To reduce CO₂ emissions in the near term, however, we also have to examine the existing processes and technologies,” insists Davor Spoljaric. “There’s a considerable potential there for measures that require relatively low investment and can be implemented rapidly.” He is referring here to increasing the use of scrap in steel production and improving energy efficiency in combustion. The increased use of oxygen in combustion processes promises both ecological and economic benefits. Fuel/O₂ combustion enables an immediate first step toward lower CO₂ emissions and also prepares the way for H₂/O₂ combustion as soon as an adequate supply of hydrogen becomes available at acceptable prices. It has already been used for years now in a wide range of processes – including ones outside of metallurgy. The use of oxygen results in significantly lower CO₂ emissions as well as a smaller waste gas volume with higher CO₂ concentration, which in turn allows for more efficient carbon capture.
These processes open up low-investment options for achieving fuel savings of 20-60 percent and lowering the steel industry’s worldwide CO₂ emissions by up to 200 metric megatons per year. Initial trials studying the injection of hydrogen into blast furnaces have also demonstrated considerable potential for reducing carbon footprint: 20-30 kilograms of H₂ per metric ton of steel can reduce CO₂ emissions by 10-15 percent.
“As more green hydrogen becomes available, its share in this process can be continuously increased, which will further reduce emissions,” explains Davor Spoljaric. “As flammable and reductive gases, natural gas and hydrogen are handled in a very similar manner. Handling them is part of Messer’s core business.”
❝
We engineer and produce the control systems that supply the media along with the burners to optimize the processes.
Dasen Karmelic, the manager of Messer Competence Center for High Temperature Processes
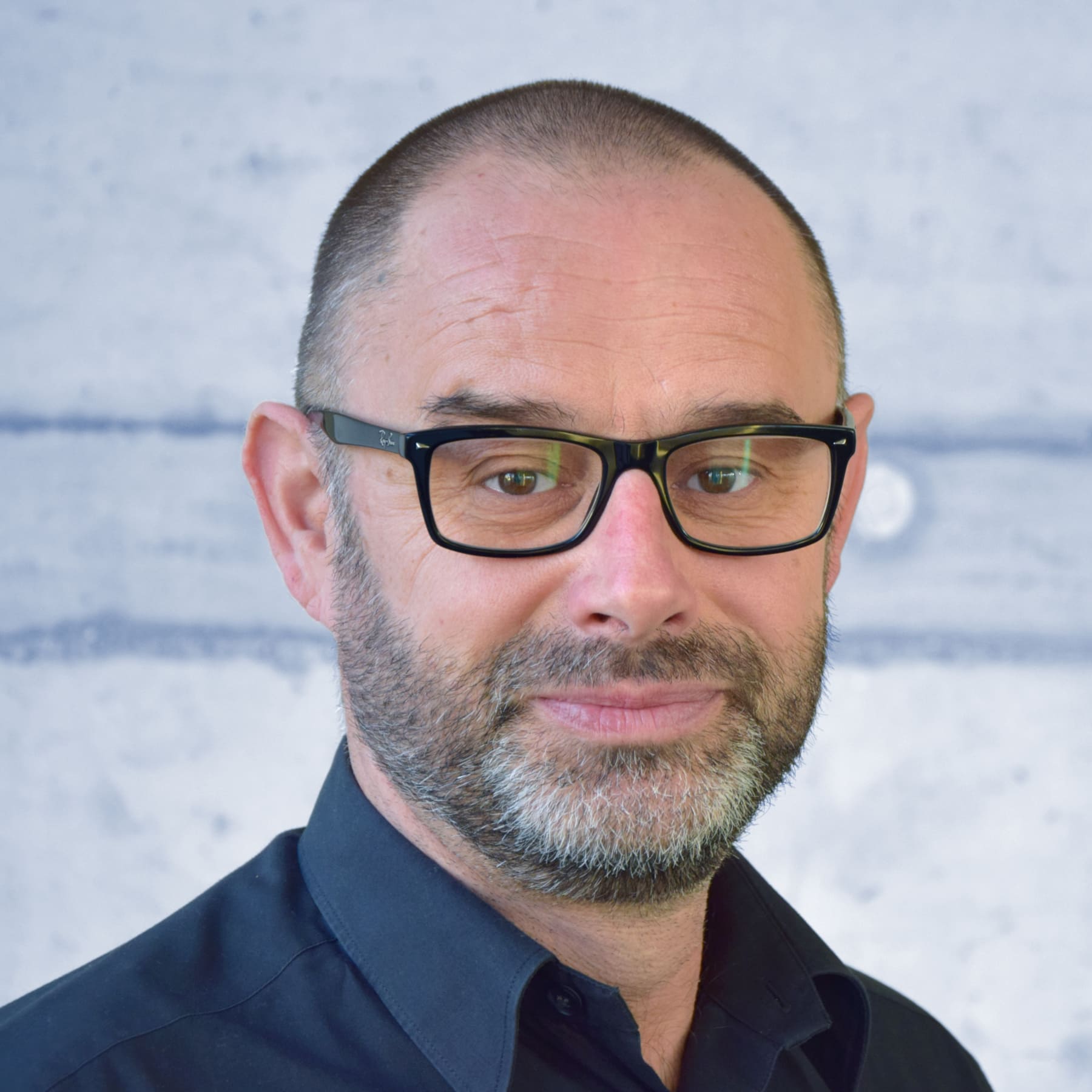
Competence center for practical solutions
Messer maintains a competence center for high-temperature processes in Gumpoldskirchen, Austria. Every day, employees there study ways to make combustion and energy transfer more efficient. “We engineer and produce the control systems that supply the media along with the burners to optimize the processes,” explains the center’s manager, Dasen Karmelic. “Prior to delivery, we subject the equipment to extensive practical testing while further developing the technologies at the same time. In recent years, we’ve been working very hard on H₂ combustion. That’s how we know that some of our burners can also burn hydrogen or can be optimized for hydrogen service without much additional cost.”
The competence center’s daily routine focuses primarily on the oxygen-based oxyfuel process. “In natural gas combustion with air admission, we can reach a final temperature of 1,980 degrees Celsius,” explains Dasen Karmelic. “When we completely replace the air with oxygen, it’s 2,600 degrees. That’s a tremendous increase in efficiency. When retrofitting existing units, it’s not always possible to convert to 100% oxygen combustion. We determine what’s possible, use our engineering expertise to optimize combustion, and minimize both fuel and CO₂ emissions.”
◤
Steel from direct reduction (DRI)
Iron ore contains iron oxides. To extract valuable iron from it, reduction must be used to remove the oxygen from this compound. In the blast furnace, the oxygen combines with the synthesis gas, which forms as the coke burns and consists for the most part of carbon monoxide. The reduction reaction turns it into CO₂. Unlike blast furnaces, direct reduction units do not need coking coal to operate. A direct reduction unit is a shaft furnace fed with iron ore pellets, which are also reduced with a synthesis gas using the counter-current principle. The important thing about DRI is that the reduction process in the shaft oven can use not only synthesis/reduction gas (comprising hydrogen and carbon monoxide) produced from natural gas (or other C carriers), but also just plain hydrogen generated from water electrolysis. Using natural gas as the reduction agent already significantly reduces the emission of fossil carbon dioxide to about one ton of CO₂ per ton of steel.
The DRI process produces sponge iron, a porous, sponge-like product with an iron content of 92-95 percent. The sponge iron is subsequently processed further in the electric arc furnace into crude steel by smelting and slag metallurgy. However, the DRI process with hydrogen requires a higher-quality iron than for the classic blast furnace route. An integrated process with net zero emissions requires very large quantities of hydrogen: about 80 kilograms per metric ton of steel (50-70 kilograms for direct reduction, 2-4 kilograms in the electric arc furnace and 10 kilograms in the reheating furnace).
Further information about the steel industry and decarbonization is available at: greensteelworld.com