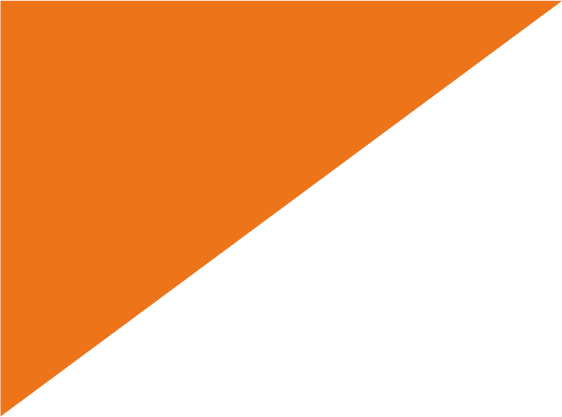
Focus on Cylinder
Stainless steel cylinders as new packaging for high-purity gases
gas aktuell No. 38, 1990
Photo: The stainless steel cylinder, a new storage and transport medium for gases
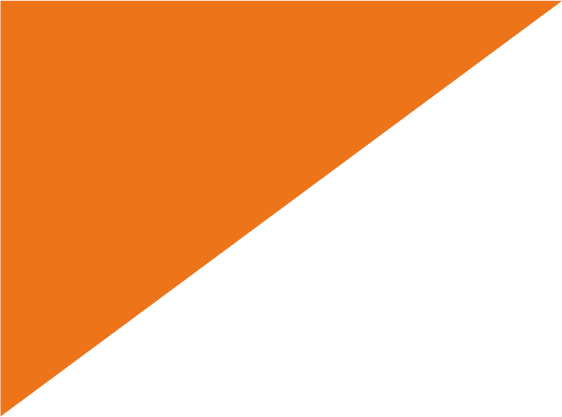
Focus on Cylinder
Stainless steel cylinders as new packaging for high-purity gases
gas aktuell No. 38, 1990
Photo: The stainless steel cylinder, a new storage and transport medium for gases
Messer Griesheim’s newly commercialized stainless steel cylinder closes a gap in the logistics concept for high-purity gases and for extremely low-particle gas grades (Megapur® standard). Unlike conventional cylinders, the new stainless steel cylinder features high-quality workmanship, from the quenching and tempering of the interior surface to electropolishing.
The wide neck provides easy access to the interior of the cylinder. The valve head, which can be unscrewed, has been completely redesigned: It can achieve significantly higher sealing values than were possible in the past. The gas inside has no contact with threaded surfaces. This also prevents any thread abrasion residues from entering the cylinder.
Material concerns
Made of low-alloy carbon steel, the compressed gas cylinders used up until now presented rather unfavorable performance relative to particle purity. For that reason, Messer Griesheim worked with the Mannesmann pipe mill to develop a stainless steel cylinder, which is available in a high-pressure and a low-pressure version. Pure austenitic chromium-nickel steel (1.4306) with limited carbon content that is not stabilized (titanium, niobium) is used for the low-pressure cylinder. This rustproof stainless steel has a high level of corrosion resistance. The low carbon content of < 0.03 % provides excellent weldability. The precipitation of chromium carbides in the heat-affected zone is excluded. The chromium content as element responsible for corrosion resistance is 18.5 %. The nickel content is 9.5 %. Nickel improves the general corrosion resistance during the forming process (conversion to martensite). A rustproof austenitic/ferritic chromium-nickel-molybdenum specialty steel (1.4462) was selected as the material for the high-pressure cylinder. Along with its very good mechanical properties, this steel is characterized by its resistance to chloride-induced transcrystalline stress cracking corrosion. Its high chromium content and, in particular, its molybdenum content also make it extraordinarily resistant to pitting and crevice corrosion. The duplex microstructure gives the steel both high stress cracking corrosion resistance and high mechanical strength. The good weldability is achieved through a well-balanced chemical composition that provides a sufficiently large quantity of austenite in the heat-affected zone, thereby preventing harmful carbide precipitations.
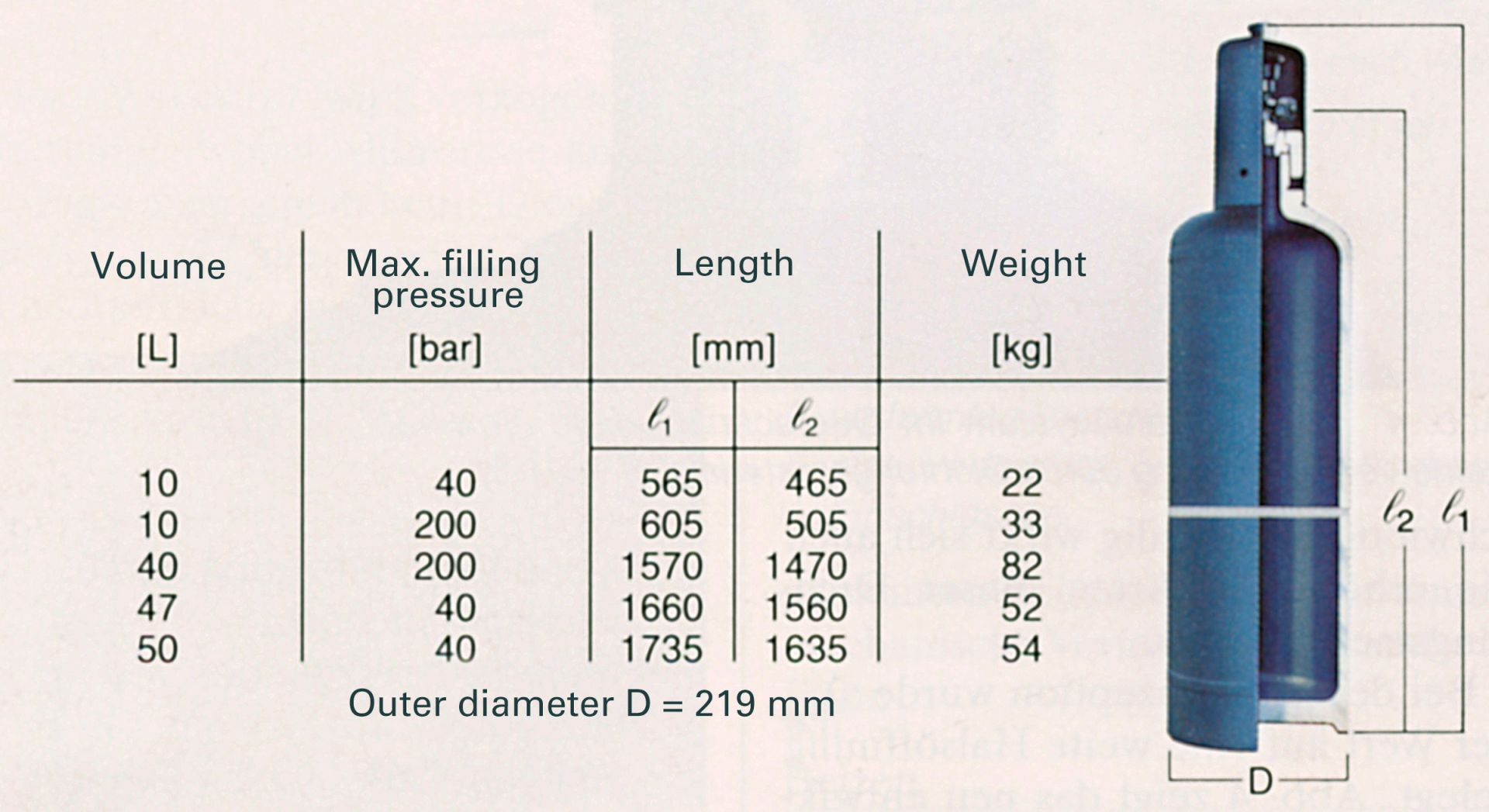
Dimensions and weights
Design features and equipment
An important requirement in the material selection was good weldability. This made it possible to design a welded tank in which the base and head sections are not subject to distortion. The cylindrical part of the tank is made of welded plate with a longitudinal weld seam. Tank base and cylinder head consist of forged parts whose interior and exterior surfaces are machined. Unlike with conventional steel cylinders, this provides a specifically defined surface quality. After completion of the appropriate welding preparation, head and base sections are welded to the cylindrical part. Particular attention was paid to the design of the closure system. The neck of a conventional cylinder has an internal conical thread for the valve (Ø 28.8 mm). A plastic tape is typically used as seal material. The disadvantages of this type of closure are obvious: Metallic abrasion residues and sheared off seal materials end up causing particulate contamination in the cylinder. Moreover, the small neck opening makes inspection and maintenance of the interior more difficult. The increased leakage rate of this sealing method also has a detrimental effect. In the new design, a wide neck opening was given high priority. It consists of a combination of a union nut with external threads, a carrier plate for the valve, and a metallic seal ring.
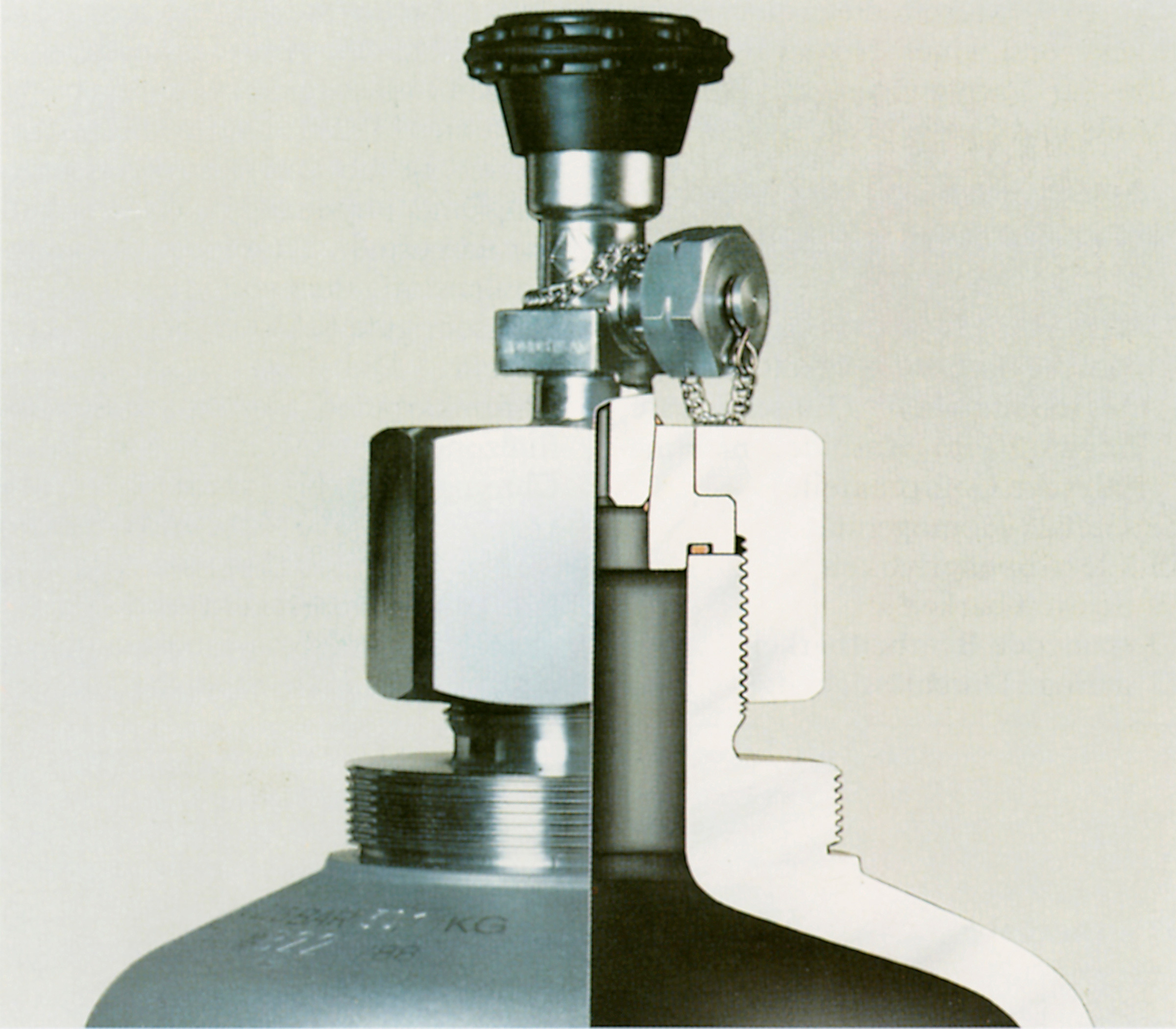
Cutaway view of the connection system: No media-contact threads, no contamination by seal material.
The proven stainless steel membrane valve (model V 6) makes it possible to use the metallic sealing VCR connector system on the side nozzles. As a result, the entire supply system can be fitted with metallic seals. All internal parts of the valve are electropolished.
Conclusion
Due to its construction, equipment, material selection and carefully matched surface treatment, the stainless steel cylinder presents numerous advantages. Those are decisive advantages when using reactive gases in the electronics industry or in other applications where extremely high-purity gases are required. Other compressed gas cylinders, e.g. the aluminum cylinder, offer some of these positive characteristics, but only the stainless steel cylinder combines the full spectrum of benefits, ranging from corrosion resistance to minimized particulate contamination.