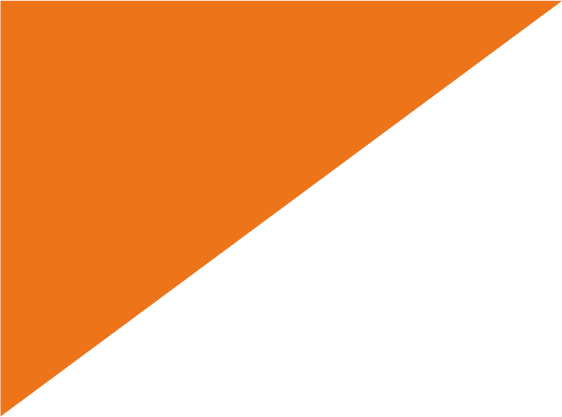
Using Gases
Oxygen – an economical alternative for increasing the melting capacity of electric furnaces
gas aktuell No. 5, 1984
Photo: Electric arc furnace with integrated natural gas-oxygen burners
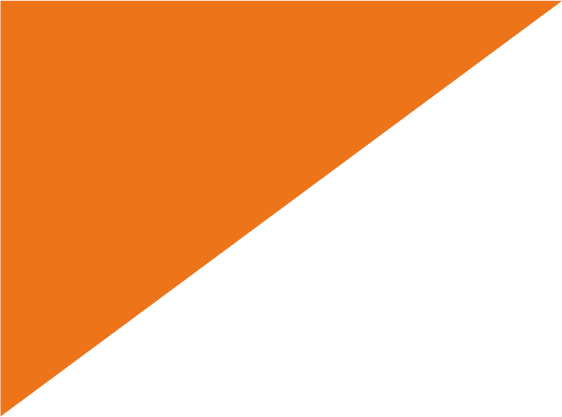
Using Gases
Oxygen – an economical alternative for increasing the melting capacity of electric furnaces
gas aktuell No. 5, 1984
Photo: Electric arc furnace with integrated natural gas-oxygen burners
Oxygen burners operated with gas or oil are an economical alternative to shorter melting times in electric furnaces with insufficient electrical power. Besides increasing melting capacity and possibly bridging power blockage periods, a reduction in the total energy consumption has been observed. Substoichiometric burner adjustment generates a reducing atmosphere in the furnace chamber, in which even high-alloy steels can be melted with low slag formation.
Electric steel production in arc furnaces and induction furnaces has been widely practiced since its beginnings at the start of this century. Along with the production of high-alloy steel grades, more and more carbon steel grades are melted especially also in electric arc furnaces today. Because melting the scrap takes by far the most time within the overall melting operation, shortening the melting time can raise the overall melting capacity of the furnace. Due to generally insufficient electrical power and transformer capacities of many furnaces, raising their overall melting capacity in the near term is impossible or would incur high investment costs. For that reason, the use of additional gas-oxygen burners or oil-oxygen burners is an economical alternative. Along with lower fixed costs per metric ton of molten material – due to the higher melting capacity – power blockage periods, which lead to very high prices for peak power demands, in particular, can be bridged. Electrical energy consumption can also be reduced.

Exhaust gas temperature of an electric arc furnace with and without burner operation
Burner design
Apart from the service weight and the available electrical power, the burner capacity required for a given melting time reduction and the service life of the burner essentially depend on the quality and fragmentation of the scrap to be processed. Therefore, the theoretical calculation of the burner setting can only be an approximation. The most favorable setting must be determined by a test run on the installed unit. The best melting results are achieved with a charge material with high specific surface area and low bulk density. Those conditions permit a convective heat transfer to make the best use of the large temperature difference between flame and charge material. Because specifically carbon, silicon, manganese and, on additional alloy elements, chromium and vanadium, are burned in an oxygen-rich furnace chamber atmosphere when melting high-alloy steels and cast iron, the burner must be substoichiometrically adjusted. When adjusting the flame, the furnace geometry must also be taken into consideration, because any damage to the brickwork due to flame impingement would reduce the service life of the lining. The burners on the electric arc furnace are installed in a way that directs the flames between the electrodes. This imparts additional heat to the scrap in the “cold spots,” thereby providing more uniform energy distribution in the furnace chamber. The number of burners used depends on the size of the furnace, the service weight and the accessibility of the furnace. For induction furnaces, one burner installed in the center of the furnace lid suffices in most cases. Specifically for induction furnace applications, Messer Griesheim uses self-cooling burners, because a defective cooling water jacket on a water-cooled burner installed in that configuration poses a high hazard potential. The sound level of these self-cooling burners falls within the noise level of a normal foundry. The absence of water cooling reduces the weight of the burner, which facilitates burner operation.
Operating experience with production units
Numerous tests were already conducted in electric arc furnaces in the past. The following is a description of the operating experience with a natural gas-oxygen burner system in a production facility.
At 353 kW/t of steel, the installed transformer capacity is at the lower limit. Some tests showed that the best melting capacity at low power consumption was achieved with a burner capacity of 249 kW/t of steel, whereby the two self-cooled burners were in operation for no more than 15 minutes. With this setting, the overall melting capacity increased by 19.1 % per batch. Taking into account the necessary non-productive times in the furnace, that raised the number of batches in two-shift operation from 7 to 8 batches/day. The total energy consumption was reduced from 590 kWh/t of steel to 566 kWh/t of steel. Therefore, the furnace efficiency was increased from 68 % to 72 %. No change was measured in the service life of the furnace refractory lining (approx. 315 batches) or the electrode consumption (approx. 5.8 kg/t). In an electric arc furnace with two self-cooled natural gas-oxygen burners, the left burner was not directed towards the center of the furnace. After the subsequent adjustment of the burner, the melting time was further reduced. In the flame zone, part of the scrap melted down and/or was preheated at high temperatures. No significant preheating of the scrap has been observed yet in the furnace zone which was not reached by the flames. The installation of a third burner increased the melting capacity by about another 10 %. Due to the low weight of the burners, they are inserted and withdrawn from the furnace manually on this unit. Larger capacity burners are inserted and withdrawn by means of a pneumatic or hydraulic system. The ignition and monitoring of the burners are electrically interlocked to operate only inside the furnace and fully automatically controlled by an electrical control cabinet.
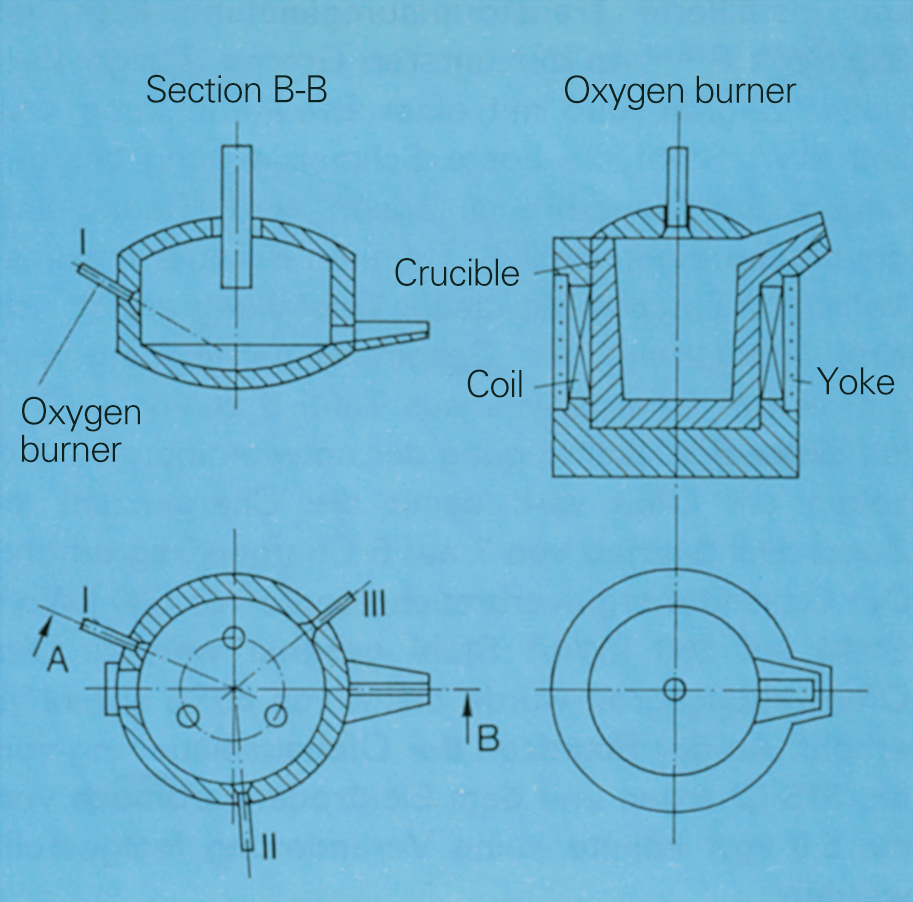
Schematic representation of the burner configuration in electric furnaces (left: electric arc furnace, right: induction furnace)
An electric interlock of the electric arc furnace additionally prevents the burner from being switched on unless an arc is present. This automatic sequence and the monitoring of the burner functions ensures the greatest possible safety during burner operation and adds very little workload for the operator.
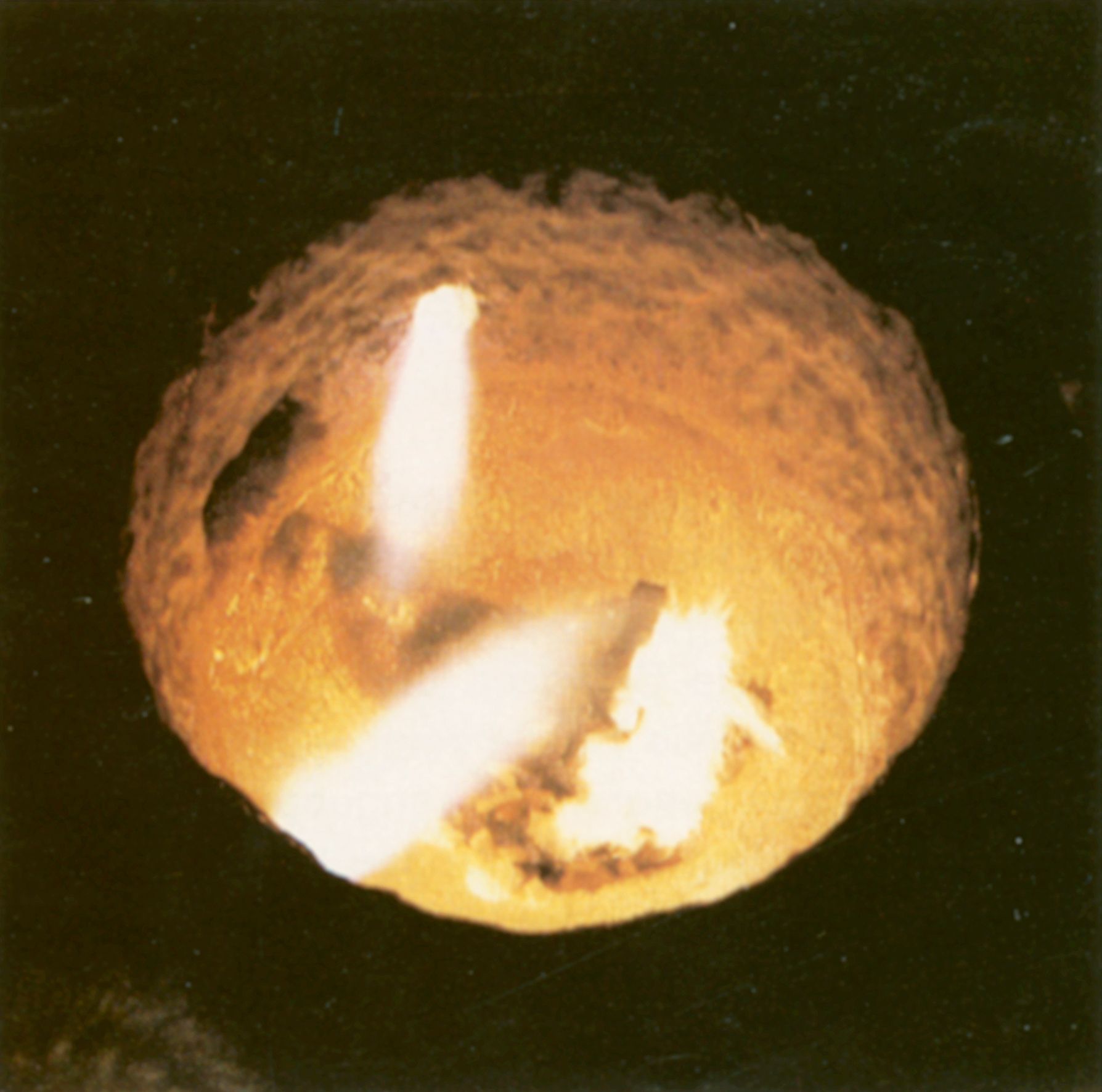
Flame pattern in the empty furnace vessel
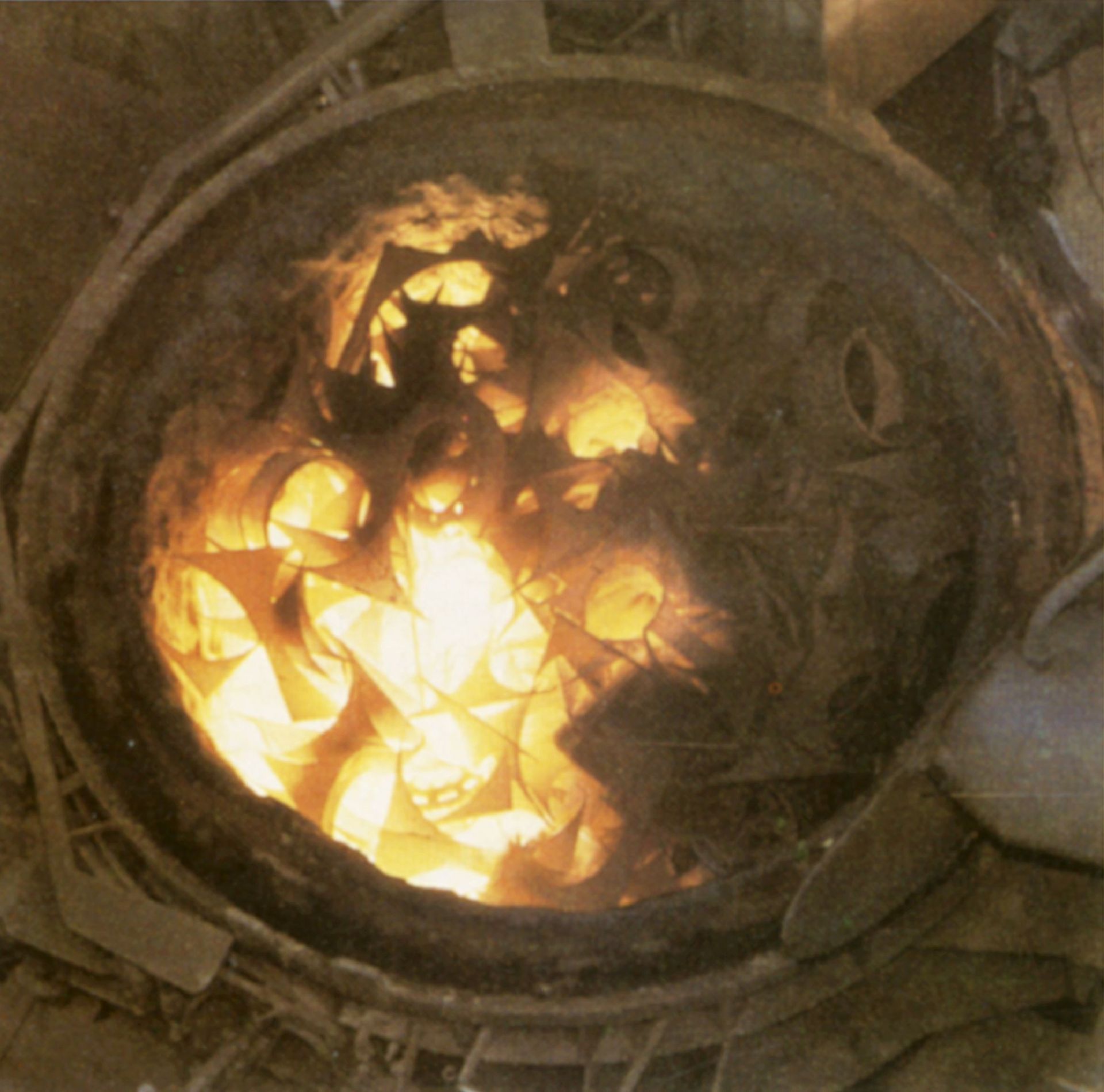